why your Business might need a Metal Cold Saw
In the highly competitive world of sheet metal and steel fabrication, businesses must continually invest in tools and technologies that improve efficiency, precision, and overall productivity. Among these tools, the metal cold saw stands out as a versatile, durable, and cost-effective option for cutting metals with high accuracy and minimal waste. Whether you are an established fabrication business or a growing enterprise, a MEP cold saw can provide numerous benefits that directly impact your bottom line. In this article, we explore the key reasons why investing in a cold saw is a strategic move for any fabrication business.
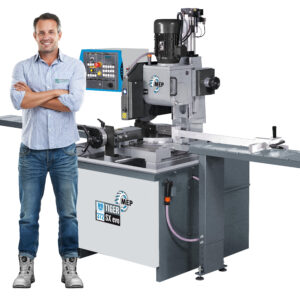
1. Superior Cutting Precision
Metal cold saws use a circular blade with hardened teeth to deliver clean and precise cuts. This precision is critical in sheet metal and steel fabrication, where accuracy directly influences the quality of the finished product. Unlike abrasive saws that can leave uneven edges or burrs, cold saws produce smooth, straight cuts that often eliminate the need for additional finishing work. This not only saves time but also ensures that pieces fit together perfectly in assembly.
For businesses working on projects with tight tolerances, such as automotive components, architectural elements, or industrial machinery, the precision offered by a cold saw is invaluable. The ability to achieve consistent results across multiple cuts enhances product quality and customer satisfaction.
2. versatlity across materials and shapes
Cold saws are incredibly versatile, capable of cutting a wide range of materials, including:
- Mild steel
- Stainless steel
- Aluminum
- Brass
- Copper
- Other non-ferrous metals
In addition to accommodating various materials, cold saws can handle diverse shapes, such as bars, pipes, tubes, and sheets. This makes them ideal for fabrication businesses that deal with a variety of projects and client requirements. Moreover, many cold saws offer adjustable angles for miter cuts, enabling greater flexibility in creating complex designs or custom components.
3. high quality edges with minimal post-processing
One of the standout features of a MEP cold saw is their ability to produce clean edges with minimal burr formation. Unlike abrasive cutting methods, which often require extensive post-cut deburring or grinding, cold saws leave edges smooth and ready for immediate use. This reduces the need for secondary processing, saving both time and labor costs.
For fabrication businesses working with high-end materials or components that demand a polished finish, the edge quality achieved by a cold saw can significantly enhance efficiency and product aesthetics.
4. reduced heat and material distortion
Cold saws operate at relatively low speeds and generate minimal heat during the cutting process. This “cold cutting” method prevents thermal distortion, discoloration, or warping of the material—common issues associated with other cutting techniques like plasma or laser cutting.
For businesses working with heat-sensitive materials or requiring precise dimensions, the lack of heat-induced changes is a major advantage. It ensures that the integrity of the material remains intact, which is especially important for structural components or high-precision applications.
5. efficiency and productivity boost
Time is money in any fabrication business, and cold saws are designed to optimise cutting efficiency. They offer faster cutting speeds compared to manual saws or other traditional methods, enabling businesses to complete jobs more quickly. Modern metal cold saws, particularly those equipped with CNC controls, can perform repetitive cuts automatically, freeing operators to focus on other tasks.
The combination of speed, automation, and minimal post-processing makes cold saws an excellent investment for improving overall productivity. Whether you’re working on small-scale projects or large production runs, a cold saw can help you meet deadlines without compromising quality.
6. long lasting durability and reliability
Cold saws are built to withstand the demands of industrial use. Their blades, often made from high-speed steel (HSS) or tungsten carbide, are designed to last longer and perform consistently across numerous cuts. Unlike abrasive saws that wear down quickly and require frequent replacements, cold saw blades offer superior durability, reducing downtime and replacement costs.
Additionally, the robust construction of cold saw machines ensures they can handle heavy-duty applications while maintaining precision. For businesses looking for a reliable, long-term cutting solution, cold saws provide an excellent return on investment.
7. lower operating costs
Operating costs are a critical consideration for any fabrication business, and cold saws excel in this area. They consume less energy compared to other cutting methods, such as plasma or laser cutters, and their blades have a longer lifespan. This reduces both energy bills and tooling expenses.
The precision of cold saws also minimises material waste, further contributing to cost savings. By delivering accurate cuts with minimal errors, businesses can maximise their material usage and avoid the financial impact of scrapped pieces.
8. enhanced safety features
Workplace safety is paramount in any fabrication environment, and cold saws are designed with operator safety in mind. Features like blade guards, secure clamping systems, and minimal spark generation reduce the risk of accidents during operation.
Unlike abrasive saws that produce high levels of dust, heat, and noise, cold saws operate more quietly and cleanly. This creates a safer and more comfortable working environment, contributing to employee well-being and productivity.
9. scalability and automation
As fabrication businesses grow, so do their production demands. Cold saws are well-suited for scalability, with advanced models offering CNC programming and automation capabilities. These features allow for precise, repeatable cuts, making them ideal for high-volume production runs.
Automated cold saws can integrate seamlessly into existing workflows, enabling businesses to scale operations without compromising efficiency. For companies looking to future-proof their operations, investing in a CNC cold saw is a smart choice.
10. Competitive advantage
In a competitive industry, delivering high-quality products on time and within budget is key to staying ahead. The precision, efficiency, and versatility of a MEP cold saw can give your business a significant edge. By reducing lead times, minimising waste, and consistently meeting customer expectations, you can enhance your reputation and attract more clients.
11. environmental benefits
Sustainability is becoming increasingly important in manufacturing, and cold saws align with eco-friendly practices. Their energy-efficient operation and minimal material waste contribute to a smaller environmental footprint. For businesses looking to adopt greener practices, cold saws represent a practical step toward sustainability.
conclusion
Investing in a metal cold saw is a strategic move for any sheet metal and steel fabrication business. From delivering precise cuts and clean edges to boosting productivity and reducing costs, cold saws offer a wide range of benefits that directly impact your bottom line. Their versatility, durability, and advanced features make them an indispensable tool for businesses looking to improve efficiency, enhance product quality, and stay competitive in a demanding market.
Whether you are focused on small-scale custom projects or large-scale production runs, a cold saw can help you meet your goals with greater efficiency and reliability. By incorporating this essential tool into your operations, you can take your fabrication business to the next level, ensuring long-term success and profitability.